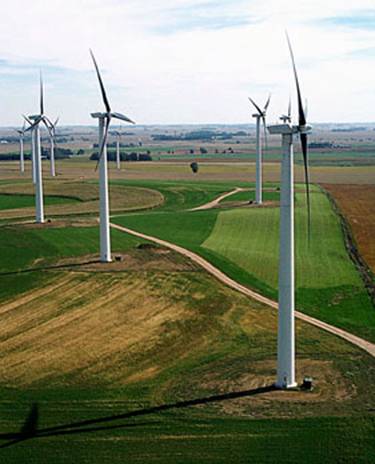
All wind turbines are equipped with a certain power control feature in case the speed of the wind is too high or too low and to have a frequency coherent with the grid. The traditional and the simplest and least expensive method in this respect is a system of natural limitation known as “stall”. The blades are mounted directly on the hub at a fixed angle. When the wind speed is higher than the operational speed, the blades begin to stall.
This system regulates the power by stalling the blades when a rated power is attained. It is simple and relatively reliable, but it misses precision because it depends on the air density and of the roughness of the blades.
The second method modern wind turbines use to control power is the pitch-controlled system, which is very precise; it can control and adjust the angle of the blades several times per second if necessary. Blade pitch control is, therefore, the system which, by regulating the blade pitch angle, turns (pitches) the blades so they can take maximum advantage of the wind and, at the same time, in case of very high wind speed it functions as a brake, adjust the angle blade so that the wind goes through. Also, the increased interest in pitch system is given by the increase of the rotor size.
As mentioned above, these pitch systems continuously control the speed, when it is too high they lower the blade speed rotation and in case of low wind speed they increase the rotation speed. Therefore, pitch systems are extremely useful; they “improve the efficiency of wind energy conversion and power generation stabilityâ€. Pitch systems are usually equipped with an electrical motor, a gearbox and an electro-mechanic actuator. There are two types of pitch systems: hydraulic and electromechanical.
Hydraulic pitch systems
In such systems, hydraulic actuators (mechanical devices that use hydraulics to convert energy into a linear movement) are used to control all blades together, rotating the blades around their axis. The configuration of hydraulic systems has the actuator work against a spring thus in case of hydraulic power failure the blades stop. The hydraulic pitch system has some important advantages: safer operation due to fail-safe function, a longer life, large driving power, and robust backup power.
Electromechanical pitch systems
Electromechanical systems are self-contained and as they don’t have hydraulic sockets, they reduce the maintenance operations and consume less power as they do not need pumps. The electromechanical pitch system is equipped with a motor, a gearbox (bringing the motor to the desired speed), bearings, internal ring gear and pinion gear which are also used to adjust the pitch angle. “The use of electric motors can raise the responsiveness rate and sensitivity of blade pitch control.â€
They have a battery-reserve in case of a power failure. These systems are more efficient and more eco-friendly since they cannot cause hydraulic oil leaks. There is a sensor for wind which measures the wind speed and direction (several times per second), and based on a control algorithm the decision of how much the blades turn is made: “when the power output becomes too high, it sends an order to the blade pitch mechanism which immediately pitches (turns) the rotor blades slightly out of the wind.
Conversely, the blades are turned back into the wind whenever the wind drops again. On a pitch controlled wind turbine, the computer will generally pitch the blades a few degrees every time the wind changes in order to keep the rotor blades at the optimum angle in order to maximize output for all wind speeds.â€
Individual pitch control
Because each blade experiences different loads at different rotation speeds, the technology had to be improved so that each blade had its own pitch system. It is also important to have an individual pitch control as the wind turbines become bigger and more complex. This new technology harmonizes the loads caused by different wind speeds variations.
The individual pitch control system controls and regulates the angle of a blade several times per rotation and thus a very important reduction in operational loading can be achieved, by a range of different algorithms: “This is a multivariable control problem, in which several inputs (including measured loads) are simultaneously processed to generate three pitch actuator demands, initial work concentrated on the use of so-called ‘LQG’ or linearquadratic-gaussian control design techniques, these being among the simplest of the ‘modern’ control design methods which are directly applicable to multivariable problems.â€
The clear advantage is the fact that the loads from the blades and other components is managed and reduced, the efficiency and yield will increase, and later expenses or maintenance operations will be diminished.
Source: Offshore Foundations for Wind Turbines
You should follow us here.
up to which spped we can get the power in case of gusty winds?